Optimize Welding Stability: Trust Our Inspection Service
Optimize Welding Stability: Trust Our Inspection Service
Blog Article
Unveiling the Diverse Variety of Welding Services and Their Benefits
As industries continue to demand and advance accuracy in their manufacturing processes, the value of welding solutions has actually become significantly obvious. From the convenience of arc welding to the performance of MIG welding, and the detailed work achieved with TIG welding to the precision of laser welding, the selection of welding methods available is substantial.
Sorts Of Welding Provider
One typical kind is MIG welding, additionally understood as Gas Steel Arc Welding (GMAW), which uses a wire electrode to join steels with each other. An additional widely utilized technique is TIG welding, or Gas Tungsten Arc Welding (GTAW), which utilizes a non-consumable tungsten electrode to produce a specific and clean weld.
Additionally, there is Stick welding, or Protected Steel Arc Welding (SMAW), which is known for its simplicity and performance, especially in exterior or windy conditions. There is Flux-Cored Arc Welding (FCAW), which is a flexible procedure suitable for thick products and can be used in both automated and semi-automatic applications.
Benefits of Arc Welding
Arc welding supplies a multitude of advantages that provide to different commercial requirements and demands. Additionally, arc welding is recognized for its high welding speeds, which can dramatically increase performance in producing processes.
Another trick benefit of arc welding is its ability to create solid and sturdy welds. Arc welding also produces clean and accurate welds, decreasing the requirement for added ending up work.
Benefits of MIG Welding
With an emphasis on effectiveness and toughness in welding processes, MIG welding provides an unique collection of advantages that match the versatility and toughness found in arc welding. MIG welding, or Gas Metal Arc Welding (GMAW), is recognized for its speed and ease of use. The process involves feeding a wire electrode via a welding gun, which is then thawed and made use of to join the base products together. Among the essential advantages of MIG welding is its high welding rates, making it a recommended selection for tasks that need quick turn-around times.
Additionally, MIG welding generates tidy welds with very little splatter, minimizing the demand for extensive cleanup after the welding process. The versatility of MIG welding enables welding a vast array of products, consisting of light weight aluminum, stainless steel, and light steel. This adaptability makes MIG welding ideal for various sectors, from automobile to building.
In addition, MIG welding is known for its high deposition prices, implying even more product can be transferred in a much shorter quantity of time compared to various other welding processes. This causes raised productivity and cost-effectiveness for tasks that need huge volumes of welds. On the whole, the advantages of MIG welding make it a beneficial strategy for attaining reliable and long lasting welds across various applications.
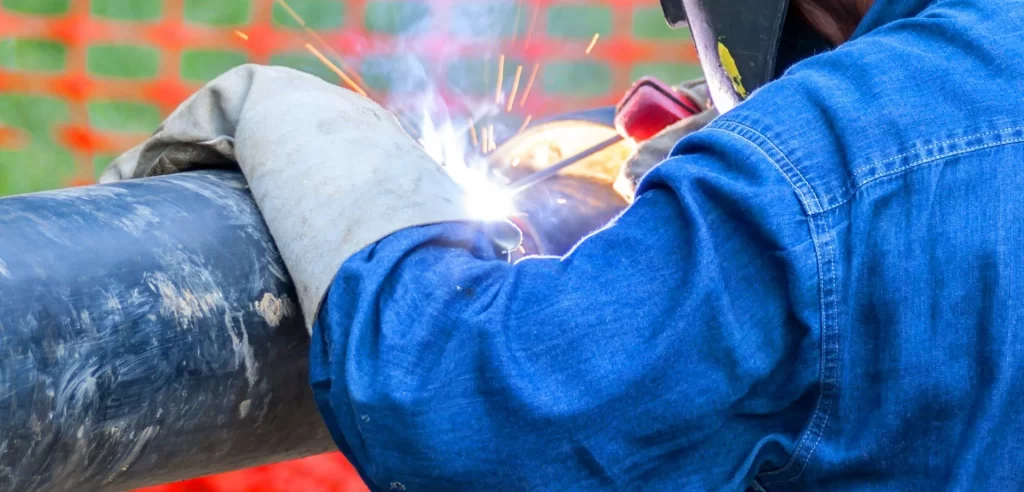
Discovering TIG Welding Benefits
TIG welding, likewise referred to as Gas Tungsten Arc Welding (GTAW), provides a distinct collection of advantages that provide to precision and control in welding applications. Among the primary benefits of TIG welding is its capability to generate top quality, tidy welds without the demand for filler product. This makes it perfect for welding slim materials where looks and precision are important, such as in the aerospace and auto industries. Furthermore, TIG welding offers excellent control over the warm input, leading to marginal distortion of the work surface.
Moreover, TIG welding can be made use of on a vast array of steels, consisting of stainless steel, light weight aluminum, titanium, and copper, making it a versatile selection for different welding jobs. The process also enables for welding in different settings, providing flexibility in challenging welding situations. Moreover, TIG welding generates see welds with exceptional toughness and honesty, making it a favored option for crucial applications where weld quality is extremely important. On the whole, the convenience, accuracy, and control provided by TIG welding make it a valuable method in the welding sector (Welding Inspection Service).
Benefits of Laser Welding
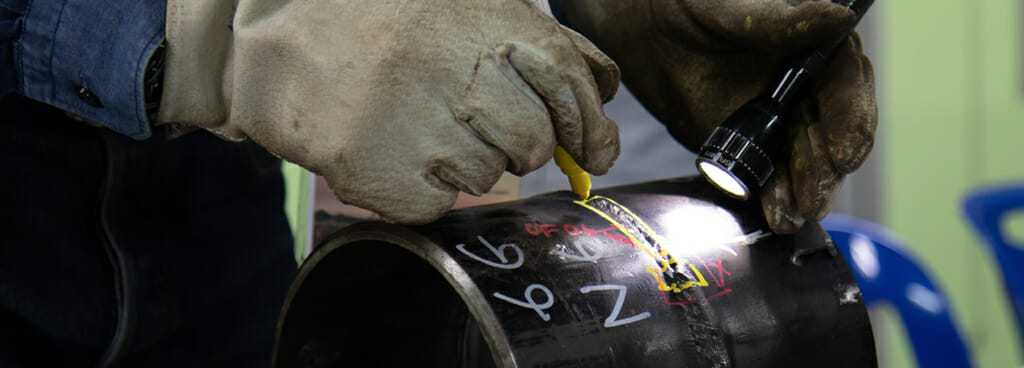
Another benefit of laser welding is its flexibility in working with a wide variety of products, consisting of metals, plastics, and also dissimilar materials. This flexibility makes laser welding appropriate for diverse industries such as automobile, aerospace, electronics, and medical devices. The non-contact nature of laser welding also reduces contamination, making it a clean and eco-friendly welding technique.
Moreover, laser welding makes it possible for complex and complex weld geometries that might be challenging to achieve with standard welding methods. This capability opens up new style possibilities and enables the production of lighter and a lot more cutting-edge components - Welding Inspection Service. On the whole, the benefits of laser welding make it a preferred option for several manufacturing applications looking for high precision and performance
Final Thought

Arc welding provides sturdy and solid welds, while MIG welding offers performance and flexibility. TIG welding makes sure accurate and clean welds, and laser welding supplies high accuracy and speed.
From the convenience of arc welding to the performance of MIG welding, and the detailed job completed with TIG welding to the accuracy of laser welding, the array of welding methods offered is vast. One common kind is MIG welding, also understood as Gas Steel Arc Welding (GMAW), which makes use of a cable electrode to sign up with metals with each other. Furthermore, arc welding is understood for its high welding speeds, which can considerably increase performance in making processes.With a focus on efficiency and longevity in welding procedures, MIG welding provides an unique set of advantages that complement the adaptability and strength discovered in arc welding.TIG welding, also understood as Gas Tungsten Arc Welding (GTAW), supplies a distinct additional hints set of benefits that cater to accuracy and control in welding applications.
Report this page